Cannabis winterization equipment consists of specialized cryogenic systems that cool cannabis extracts to temperatures between -4°F (-20°C) and -40°F/C. These systems typically feature jacketed stainless steel tanks with pneumatic mixers, polyurethane insulation, and multistage filtration technology. The equipment removes unwanted fats, waxes, and lipids from crude oil, resulting in a more refined product. Modern innovations integrate winterization with extraction processes, increasing efficiency while maintaining compliance with safety standards. Additional technical specifications reveal how these systems maximize oil purity.
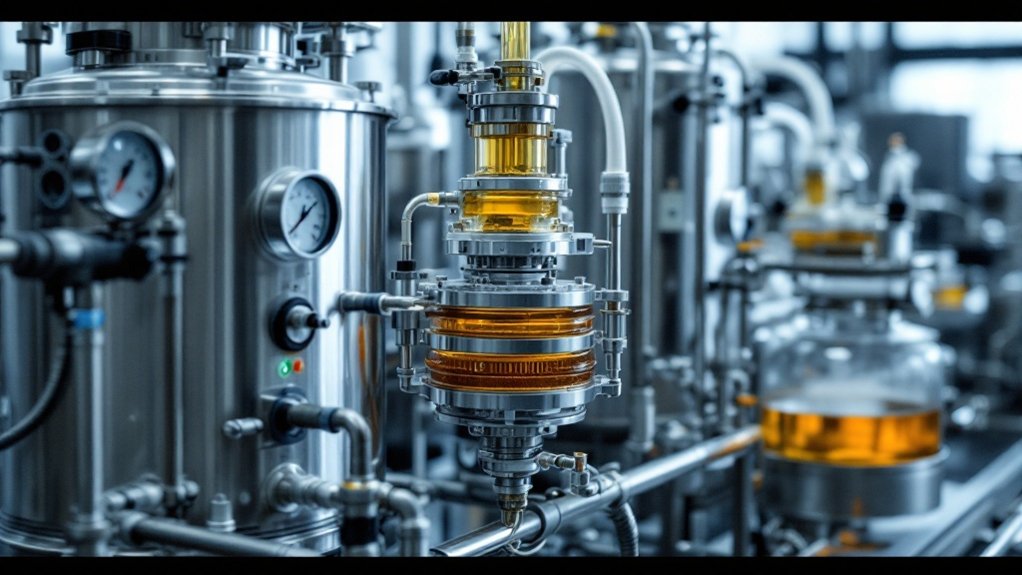
Every successful cannabis extraction operation relies on specialized equipment to produce high-quality, refined cannabis oils through the critical process of winterization. This refinement procedure, which removes unwanted fats, waxes, and lipids from crude extract, requires purpose-built systems designed specifically for cryogenic applications in the cannabis industry. Modern winterization equipment ranges from standalone components to integrated turn-key systems that combine cooling, filtration, and solvent recovery into a single streamlined process.
The foundation of winterization equipment typically consists of jacketed tanks with pneumatic mixers that can maintain the subzero temperatures necessary for proper winterization. These vessels, often constructed from AISI 304 stainless steel with TIG weld construction, feature high-efficiency polyurethane insulation to maintain temperature stability throughout the process. Air-operated systems enhance safety by eliminating electricity needs when working with flammable solvents.
At the heart of winterization lies precision-engineered stainless steel vessels, masterfully insulated to maintain the critical subzero environment.
Sophisticated systems include process temperature and pressure gauges for monitoring critical parameters, ensuring ideal conditions are maintained during each phase of the winterization process. Optimal operations require cooling the mixture to sub-zero temperatures between -20°C to -40°C for 24 to 48 hours to effectively solidify unwanted compounds.
Filtration technology represents a critical component in winterization equipment design, with most advanced systems employing multistage filtration trains. These typically incorporate both filter press systems for initial removal of precipitated compounds and 12-inch lenticular filters for final polishing of the winterized oil. The filtration media can often be swapped to accommodate additional processing requirements such as color remediation, providing flexibility for manufacturers working with varying input materials.
Innovations in the industry have led to the development of in-line winterization processes where crude extract is winterized during the extraction phase. Systems like the CRYOEXS 400 and 800 integrate winterization directly into the extraction process, while ultra-cold closed-loop extraction systems can sometimes eliminate the need for separate winterization entirely. These technological advances considerably increase throughput and efficiency for large-scale producers.
Many modern winterization systems operate entirely on air power, requiring no electricity for operation—a key safety feature when working with flammable solvents. Additional operational features include clean-in-place integration with spray balls for system cleaning, pressure regulators for controlling air feeds, and stainless steel butterfly valves for precise flow control.
Equipment manufacturers increasingly design their systems to meet rigorous compliance standards, including PSI certification for multi-state operations and UL listed control panels for electrical safety. As the cannabis industry matures, winterization equipment continues to evolve toward greater automation, efficiency, and integration with other processing stages.
Frequently Asked Questions
What Temperature Range Is Optimal for Cannabis Winterization?
The ideal temperature range for cannabis winterization typically falls between -20°C and -40°C (-4°F to -40°F).
This temperature threshold is essential for proper precipitation of unwanted compounds such as lipids, waxes, and fats from the cannabis extract.
The process generally requires 24 to 48 hours of consistent cooling to achieve effective separation.
Temperature selection within this range may vary based on solvent choice, extract composition, and specific desired outcomes.
How Long Does the Winterization Process Typically Take?
Standard cannabis winterization typically takes 24 to 48 hours at temperatures between -20°C to -40°C. The duration allows waxes to fully precipitate from the solution.
Lower temperatures, ideally approaching -80°C (-112°F), can accelerate this process substantially. The timeline varies based on extraction technology, solvent ratios, and equipment efficiency.
Modern automated systems have improved processing times, but proper winterization remains a time-intensive step that guarantees higher quality final products through complete separation of unwanted compounds.
Can I Reuse Ethanol After Winterization?
Yes, ethanol can be reused after winterization through a recycling process.
Distillation systems recover approximately 95% concentration of the original ethanol, making it economically beneficial for commercial operations.
The recycled ethanol must be reconditioned and tested before subsequent use.
This process is particularly efficient because ethanol’s polar properties remain intact after recycling, allowing it to maintain effectiveness in separating cannabinoids from undesirable substances in future winterization cycles.
Does Winterization Reduce Potency of Cannabinoids?
Contrary to reducing potency, winterization typically increases cannabinoid concentration in cannabis extracts.
The process removes unwanted plant materials, fats, and waxes that dilute the cannabinoid fraction, resulting in a more concentrated final product.
Studies have shown winterized oil contains higher THC content compared to unwinterized crude (1.63% vs 1.55% in one example).
Is Laboratory-Grade Equipment Necessary for Small-Scale Winterization?
Laboratory-grade equipment is not strictly necessary for small-scale winterization processes.
Basic winterization can be effectively performed using commonly available items such as beakers, consumer-grade freezers, and simple filtration setups.
While professional equipment enhances precision, consistency, and efficiency, small producers can achieve satisfactory results with alternative setups.
As production volume increases, however, upgrading to laboratory-grade chillers, vacuum filtration systems, and programmable controllers becomes increasingly beneficial for maintaining product quality and operational efficiency.