Regular maintenance extends the lifespan of cannabis distillation equipment. Thoroughly disassemble and clean components after each use with appropriate solvents, and inspect glassware for damage. Apply vacuum grease to seals, check for obstructions, and perform leak tests regularly. Clean cutting tools immediately to prevent residue buildup. Implement a systematic maintenance schedule with detailed documentation of all activities. Proper care of these precision instruments guarantees consistent extraction quality while reducing costly downtime.
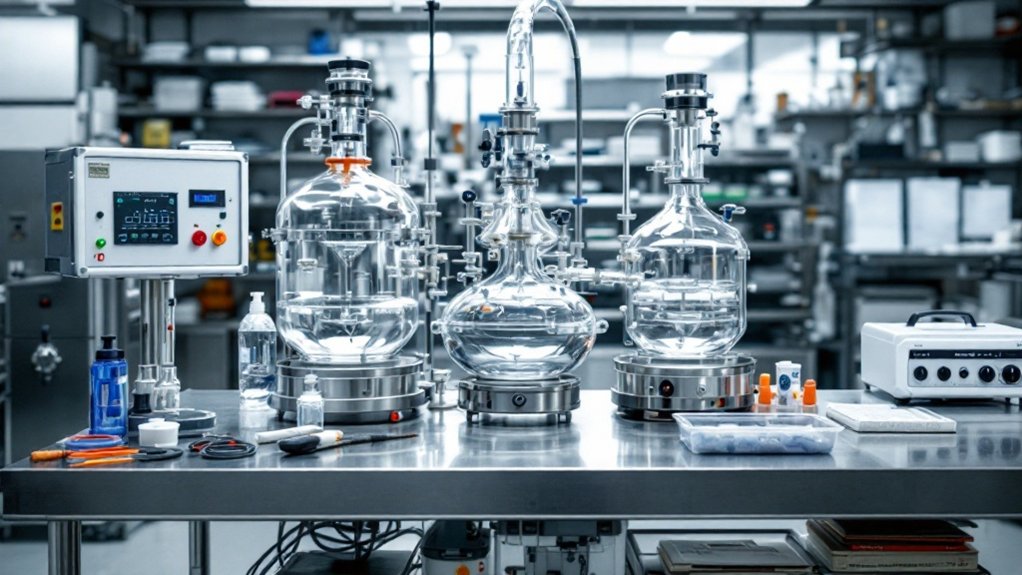
Maintaining cannabis distillation equipment properly guarantees peak performance, product quality, and operational longevity. Thorough disassembly of equipment after each extraction cycle allows for extensive cleaning of all glassware components. Operators should rinse these components with appropriate solvents to remove residual cannabis compounds before applying eco-friendly, biodegradable cleaning concentrates diluted with water. Implementing a color-coding system for cleaning tools helps prevent cross-contamination between different product lines. Ultrasonic cleaning systems provide an effective alternative that uses cavitation processes to thoroughly remove contaminants from hard-to-reach areas of distillation equipment.
Cutting tools require immediate cleaning after each use to prevent the accumulation of sticky residues that can compromise future extractions.
Never delay cleaning your cutting tools – sticky residues accumulate fast and will sabotage your next extraction process.
Vacuum systems represent vital components requiring specialized attention. Regular application of appropriate vacuum grease to seals guarantees proper functioning while preventing air infiltration. Technicians should routinely check vacuum ports for obstructions and utilize vacuum gauges to monitor system performance during operation.
Leak tests performed at scheduled intervals help maintain system integrity, while emptying oil from vacuum pumps after batch completion prevents contamination and extends pump lifespan.
Equipment longevity depends on rigorous inspection routines. Glass components must be examined for chips, cracks, or scratches that could compromise structural integrity during thermal processes. Ground glass joints require verification for proper fit and seal, while elastomeric seals and O-rings should be inspected for signs of degradation, hardening, or cracking.
Rotary mechanisms and bearings need evaluation for smooth operation to prevent catastrophic equipment failure during delicate distillation processes.
Effective maintenance relies on systematic scheduling and documentation. Creating specific maintenance calendars for each extraction system helps establish appropriate frequency for different tasks. Dedicated logbooks documenting all maintenance activities provide valuable historical data and compliance evidence.
Strategic scheduling of preventative maintenance during non-production periods minimizes operational disruptions while maximizing equipment uptime.
Inventory management plays an important role in maintenance efficiency. Maintaining supplies of replacement parts, consumables, and specialized cleaning tools ensures rapid response to equipment issues. Proper stock of vacuum grease, sealants, filters, and coolants prevents delays in maintenance procedures.
Specialized equipment requires following manufacturer-specific guidelines for cleaning and storage when not in use.
Safety remains paramount in equipment maintenance protocols. Only approved cleaning solutions should contact equipment surfaces to prevent product contamination. Disposal of used cleaning solvents must follow regulatory requirements.
Equipment should undergo safety checks before operation, verifying that all maintenance activities have been properly completed and documented, guaranteeing both equipment integrity and operator safety during subsequent distillation processes.
Frequently Asked Questions
How Often Should I Replace O-Rings and Gaskets?
Industry standards recommend replacing O-rings and gaskets in distillation equipment approximately every six months, though actual frequency depends on usage intensity and environmental conditions.
Boiling flask O-rings often require more frequent replacement due to their exposure to heat and solvents.
Visual inspections should be conducted regularly to identify hardening, cracking, or discoloration.
Equipment-specific manufacturer guidelines provide the most accurate replacement intervals, which may be shortened when harsh cleaning agents or acidic materials are processed frequently.
Can I Use Regular Cleaning Solutions for Cannabis Residue?
Regular cleaning solutions are ineffective for cannabis residue removal.
Cannabis extracts polymerize when heated, creating stubborn deposits that standard cleaners cannot dissolve. These residues require specialized biodegradable cleaning solutions with specific pH levels, such as CLN-SC75 (pH 3.5) or Elma tec clean S2 (pH <1), typically used with ultrasonic cleaning systems.
Non-specialized cleaners may damage glass components, leave harmful chemical residues, or fail to remove buildup, leading to equipment inefficiency and potential contamination.
What’s the Lifespan of a Typical Distillation Column?
A typical distillation column used in cannabis processing has an average lifespan of 1-2 years before requiring significant maintenance or replacement.
This duration varies based on operational factors such as frequency of use, running mode (batch vs. continuous), and column type.
Fractional distillation with longer columns typically requires more maintenance attention.
Regular cleaning protocols and proper storage between cycles can substantially extend equipment longevity, while contamination from residues accelerates deterioration.
Does Water Quality Affect Equipment Performance?
Water quality greatly impacts distillation equipment performance.
Mineral deposits from hard water accumulate on internal components, reducing heat transfer efficiency and potentially causing blockages in narrow pathways. These buildups necessitate more frequent cleaning cycles and can shorten equipment lifespan.
Additionally, corrosive elements in untreated water may accelerate metal deterioration, particularly in joints and seals.
Regular water quality monitoring and appropriate treatment systems help prevent these issues, maintaining ideal equipment functionality and extending operational longevity.
Are Manufacturer Maintenance Plans Worth the Investment?
Manufacturer maintenance plans typically provide substantial return on investment for complex extraction equipment. The annual cost ($25,000-$50,000) is often justified through reduced downtime, protection of warranty status, and prioritized service response.
These plans include expert inspection of critical components like seals and vacuum systems that directly impact operational efficiency. Additionally, maintenance documentation provides essential proof of compliance for warranty claims while ensuring proper training for specialized procedures that maintain both equipment performance and workplace safety.