A thorough commercial hydroponic supplies checklist should include essential components from five key categories. Systems require appropriate water culture equipment (reservoirs, pumps, filtration), growing media (rockwool, clay pebbles, coco coir), nutrient management tools (pH/EC meters, dosing systems), environmental controls (lighting, climate regulation), and maintenance supplies (cleaning agents, replacement parts). Each operation will require customization based on specific crops and scale, with proper planning preventing costly system failures and production interruptions.
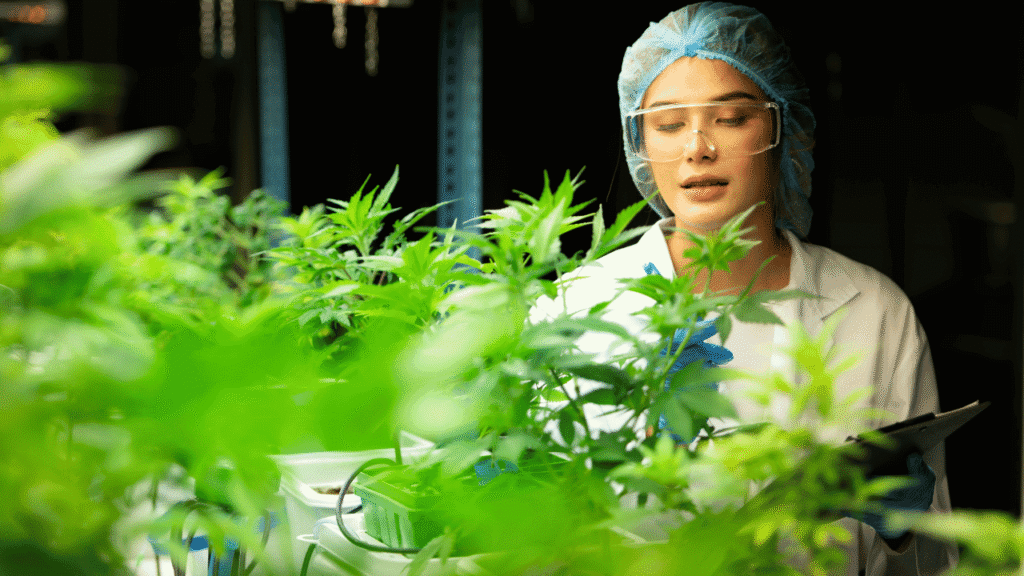
Every successful commercial hydroponic operation requires an extensive array of specialized equipment and supplies to function efficiently. The foundation of any system begins with selecting the appropriate hydroponic method, whether Deep Water Culture (DWC), Nutrient Film Technique (NFT), Ebb and Flow, Drip, or Aeroponics. Each methodology presents unique advantages and challenges, with DWC suspending roots directly in nutrient solution while Aeroponics mists suspended roots with nutrient-rich water. Commercial operations typically implement multiple systems to diversify production capabilities and mitigate risk.
Vital components for proper system function include appropriately sized reservoir tanks, water filtration systems, and climate control equipment. Air pumps paired with air stones deliver essential oxygen to plant roots in water-based systems, preventing root rot and promoting healthy growth. Water quality management requires reverse osmosis filters to remove harmful particles that might otherwise impede plant development or introduce pathogens. Large-scale commercial systems like the Flex Acre can efficiently support substantial crop production with proper equipment integration. Temperature regulation through water chillers and heaters maintains the ideal range for nutrient uptake and metabolic functions within plants. Modern hydroponic operations often integrate fertigation systems with their irrigation setup for precise delivery of nutrients directly to plant roots.
Essential hydroponic infrastructure demands precise water management and climate control to foster optimal root development and prevent pathogenic infiltration.
Growing media selection greatly impacts crop performance and operational costs. Commercial operations often utilize rockwool cubes for excellent water retention and aeration properties, while LECA clay pebbles offer reusability advantages. Coco coir presents an environmentally sustainable alternative with excellent water retention characteristics. Larger facilities typically incorporate multiple media types to accommodate different crops and growth stages.
Nutrient management forms the core of successful hydroponic production. Commercial systems employ pH testing equipment and EC/PPM meters to monitor solution parameters continuously. Automatic dosing systems deliver precise nutrient concentrations while maintaining ideal pH levels between 5.5 and 6.5 for most crops. Reservoir exchange schedules prevent nutrient imbalances and salt accumulation that could compromise plant health.
Environmental control systems regulate temperature, humidity, carbon dioxide levels, and air circulation throughout growing areas. Light systems with appropriate spectrum and intensity provide energy for photosynthesis while minimizing electrical consumption.
Maintenance protocols include regular cleaning routines, system inspection checklists, and pest management strategies that emphasize prevention. Commercial operations must balance space utilization, energy consumption, and labor requirements against projected yields when calculating return on investment for different system configurations.
Maintaining an inventory of replacement parts guarantees minimal downtime when components require servicing or replacement.
Frequently Asked Questions
What Permits Are Needed for Commercial Hydroponic Operations?
Commercial hydroponic operations typically require several permit categories.
Cannabis Cultivation through the state and zoning permits guarantee compliance with local land use designations, while business operation permits and licenses establish legal business status.
Environmental permits govern pollution control and reporting requirements.
Equipment certification is necessary through UL, FDA, and FCC standards to guarantee safety and compliance.
Special variances may be needed when operating in non-agricultural zones.
Urban farms require additional consideration regarding agricultural permissions within city limits.
How Much Technical Expertise Is Required for Maintenance?
Hydroponic system maintenance requires significant technical expertise across several domains. Daily monitoring of pH, EC, temperature, and humidity levels must be conducted with precision to guarantee peak plant health.
Operators need specific knowledge of cleaning protocols, including proper disinfection procedures for system components and reservoirs. Water management expertise is essential for scheduling changes and maintaining nutrient solutions.
Additionally, system enhancement demands understanding of photoperiods, equipment maintenance, and prevention of biological contamination from algae, bacteria, and pathogens.
Are Hydroponic Nutrients Organic-Certified?
Some hydroponic nutrients are certified organic while others are not.
Organic-certified nutrients typically derive from natural sources like compost teas, fish emulsion, seaweed extracts, and worm castings. These must comply with USDA National Organic Program standards or equivalent international certifications to carry the organic label.
However, many conventional hydroponic nutrients contain synthetic minerals and chelated elements that do not qualify for organic certification.
Growers seeking organic certification must carefully select compliant nutrient solutions and verify their approval status.
What’s the Average ROI Timeline for Commercial Hydroponics?
Commercial hydroponic farms typically achieve return on investment within 2-5 years, depending on multiple variables.
Factors influencing ROI timelines include initial capital expenditure, strain selection, operational efficiency, and market conditions.
Vertical farming configurations and year-round production capabilities further enhance ROI potential through increased yield density.